Kaizen Process Map
Kaizen is translated from Japanese as “continuous improvement”. It is one of the approaches to improve the organization's performance and a customer-oriented improvement strategy. Kaizen philosophy was first applied in a number of Japanese companies during the post-World War II recovery period. Since then, it spread around the world.
Kaizen is a philosophy and mindset encouraging improvements every day and everywhere. It is focused on small but constant changes and improvements in current work processes in order to improve all functions of a business. These improvements involve all levels in an organization, strive to make all processes more efficient. Over time this approach delivers significant results. The main purpose of Kaizen is production without losses. In addition, Kaizen implementation requires relatively small material costs.
Kaizen philosophy assumes the following: our life as a whole should be focused on continuous improvement of working methods, business processes in production, development, management, and personal efficiency. The application of Kaizen principles contributes to the development and achievement success in both professional and personal life. The sudden great changes often frighten people and cause a negative brain reaction and this can have adverse consequences. At the same time, small changes stimulate rational and creative thinking and development.
Kaizen methodology is based on the principles of personal discipline and self-improvement, customer focus, open recognition of problems, teamwork, improved morale. The formation of supportive relationships, awareness of the significance of each employee, and transfer of a certain amount of authority to each one are also among the key principles. Kaizen is a methodology realized at the great involvement of employees and contributes to their permanent self-improvement. In fact, the involvement of employees in the project has an incredible impact on the success and progress of all business processes.
According to the goal, Kaizen's introduction is realized on different levels at the company: within a team, company-wide, or personally. The method also involves comparing the plan with the result and analyzing what is happening. It assumes detecting the causes when the problems occur and eliminating these causes. Kaizen comes from the simple fact — there is no enterprise without problems and helps to solve these problems. In fact, regardless of the current state, it is suggested the following truth: perfection is unattainable and there are always ways to improve processes more and more.
Kaizen methodology is also useful for visualization processes and documenting the business work from the top-down. Each organization is based on the business model with processes. And the better you understand these processes, their functions, and their influence on the system, the more effective your organization will develop. The visualization is one of the tools helpful in understanding the business processes of an organization, detecting problems, and improving processes.
Use the idea of Kaizen continuous improvement in your company, build and visualize the business processes effectively. Design Kaizen Process Map using the ConceptDraw DIAGRAM vector diagramming software and Classic Business Process Modeling solution fast and simply. These diagrams will be helpful to detect the waste in your company and further improve the business processes.
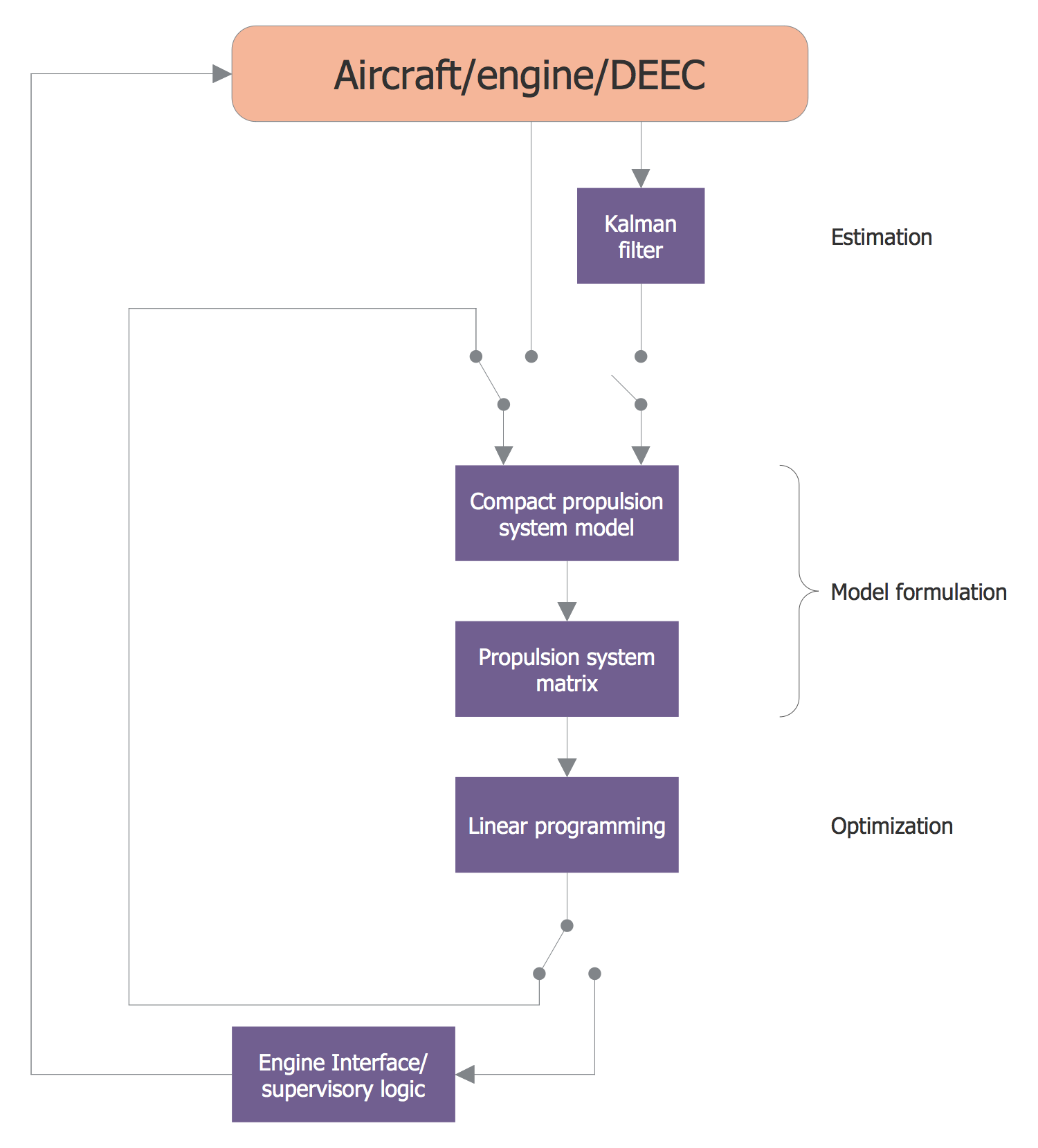
Example 1. Kaizen Process Map Design in ConceptDraw DIAGRAM
Classic Business Process Modeling solution includes a great number of ready-made vector objects and samples to easier the process of drawing the Business Process Models. Use design elements — Data Flow Diagram, Functional Flow Block Diagram, Control Flow Diagram, Flow Chart, Swimlane Diagram to illustrate the business processes of your company. Apply Kaizen methodology in order to optimize the processes and improve your business.
The sample you see on this page was created in ConceptDraw DIAGRAM software using the tools of Classic Business Process Modeling Solution. This sample was included in the Classic Business Process Modeling Solution and is available from ConceptDraw STORE. An experienced user spent 10 minutes creating this sample.
Use the Classic Business Process Modeling Solution for ConceptDraw DIAGRAM software to design your own Kaizen Process Maps fast, simply, and effectively.
All source documents are vector graphic documents. They are available for reviewing, modifying, or converting to a variety of formats (PDF file, MS PowerPoint, MS Visio, and many graphic formats) from the ConceptDraw STORE. The Classic Business Process Modeling Solution is available for all ConceptDraw DIAGRAM users.