Material Requisition Flowchart.
Flowchart Examples
Material requisition is a request generated by an internal or external organization with the goal of informing the purchasing department about the needed items and materials. The requisition can be represented as a written document on a pre-printed form or an online request in the form of an electronic document. The electronic inquisition occupies a leading position in the modern world, the paper forms are replaced by electronic ordering processes and workflows.
The requisition is actively used in business as an internal document for notifying the store about the needed goods, in medicine for making orders on medical equipment and medicaments, in industry for creation request for purchasing some items and materials, and so on.
Issuing Material Purchase Orders
A so-called “purchase order” (or PO) is a document used in commerce. It is the first official offer, which is issued and given from the buyer to his seller. In this document, the buyer indicates the type, quantity, and price of his product or service. This “purchase order” is used for controlling the purchasing of products as well as services from external suppliers.
Issuing the purchase order does not mean initiating a contract or agreement. If there is no contract, signed before the “purchase order” is issued, then it is the process of acceptance of some particular order by the seller. This acceptance forms a “contract” between the buyer of the product or service and the seller of the product or service. Within many of the companies the “purchase orders” can be used for many different reasons. These orders allow buyers to communicate simply with the sellers and to describe their intentions to sellers. These orders may also help a purchasing agent manage all of the incoming orders as well as so-called “pending” orders.
Using “purchase orders” enables to streamline the process of purchasing to some particular standard material purchase procedure. Commercial lenders, as well as financial institutes, may provide financial assistance, based on the purchase orders. There are many so-called “trade finance facilities”, which almost each of the financial institutions allows business people to use against purchase orders. It can be done before the shipment credit facility, after shipment credit one, during the trade finance facility, foreign bill purchase credit facility, bill retirement credit facility, “order confirmation” or so-called “Follow-up”.
The purpose of using the “purchase orders” is to procure the materials for a stock, procure services, direct consumption, or cover customer requirements. It can be done using all of the external resources, including procuring some definite material, which is needed to be in plants, taken from internal sources. They may also be placed when the purchasing and procurement transactions take place by taking full advantage of the existing transport conditions.
Creating a “purchase order” is usually the first step of the process of payment for the purchase. Some of the “purchase orders” may require a so-called “SKU code”. Within a so-called “ERP system”, any “purchase order” can be created manually. It also may require confirmation or it can be changed at any time in a way of its editing. Within an “ERP system”, creating a “purchase order” manually within the system may look like a step-by-step process from arranging logistics (product delivery, for example) to providing a so-called “Transaction Code”. This step-by-step process may also include involving the “materials management”, the process of “purchasing” itself and issuing the “purchasing order” itself. The type of order can always be chosen from the screen in case the computer system is used.
A so-called “vendor code lookup” may be needed to be selected for a reason of issuing the “purchase order”, as well as the information about the organization, the group and the company code. Usually “purchase orders” do not contain any contract language and they are regarded as instruments, regulated by the “Uniform Commercial Code”, which is one of the uniform acts numbers, being used in law for the purpose of harmonizing the law of sales as well as other commercial transactions within the US. Also, another similar law can be used for establishing any “purchase order” as a contract.
Although the “purchase order” is known as a kind of contract, it is common to accompany the purchase order acceptance with some legal document. This document can be “The terms and conditions” of sale, establishing additional or some specific legal conditions of some contract. In the United States of America “Federal Acquisition Regulation” states all purchase orders as they all should be issued on a fixed-price basis. Although the provision can also be made for unpriced “purchase orders”. Such unpriced purchase orders can be issued where it is impractical to obtain any pricing in advance of the purchase order issuance.
Many of the “purchase orders” are transmitted electronically with the use of the Internet, so there is no need to use paper. Nowadays, the way of issuing “electronic purchase orders” is the most popular during the process of buying goods or providing services online. “Electronic purchase orders” are also known as “E-Purchasing”, “E-Procurement”, or “E-Purchase Requisition”. Although “electronic purchase orders” are the most common nowadays, “non-electronic purchase orders” are also still used. The record of the “purchase order” in most of the business firms is still with the use of paper, so they are still in need for a proper “purchase order format”.
The term “Purchase Requisition” can be described as a document, generated by some user’s department to notify another department, which is a “purchasing” one about the product or service being ordered as well as about the quantity of products and services and the period of time they have to be delivered within. This “Purchase Requisition” may include the need for authorization in order to proceed with this purchase. “Purchase Requisition” is also known as “Requisition” or “Purchase Request”.
Example 1. Flowchart Examples (macOS and Windows)
Introduction to Material Requisition and Material Requirements Process
A requisition form is one of the documents used for accounting in different manufacturing processes. There are two main types of requisition: a purchasing requisition and material requisition and the difference between them is significant. Creating a Flowchart might help you in understanding all the details of the accounting process.
In some industrial environments, the purchasing department may be assigned with responsibility for requesting and purchasing goods. It can be a description of what happens on the production line and other processes explanation. Raw material purchase processes, where the purchasing department is also responsible for inventory management, can be a good example of that.
The basic functions of an MRP or Material requirements planning system include: inventory control, bill of material processing, and elementary scheduling. MRP helps organizations to maintain low inventory levels and is usually used for planning manufacturing, purchasing, and delivering activities. In order to make people understand this process as well as to make it clear for those who does not know about such activity, the Flowcharts can be used.
Running your own business or being responsible for making the material planning which is production planning as well as inventory control of managing manufacturing processes, you might need to create charts and flowcharts in terms of planning and so making sure you have enough materials for the following fixed period of time for using them in your production. Working in such industry, it’s important to keep your finger on the pulse of processes which are inventory control, material processing, and, of course, scheduling. Material requirements planning and material requisition planning can help you to maintain low inventory levels in a way of planning all the manufacturing, purchasing, and delivering. Purchase requisition is being used for notifying the purchasing department of products that need to be ordered, the exact quantity of them, and the period of time frame that should be given for such process. In some production businesses, this purchasing department can be in charge of requesting and purchasing all necessary goods.
Role of Flowcharts in Material Requisition
In order to describe purchase requisition you can create a Material requisition flowchart or a Requisition process flow chart. Flowcharts are the best visual method for dividing a large and complicated procedure into several little clear pieces. The main value ability of an effective Flowchart is its simplicity. Material requisition flowcharts are used to document the process of relationships between the different departments and the purchasing department within an organization. The flow chart gives a step-by-step guide on how the procurement process of the materials necessary for the functioning of the organization is carried out.
The modeling of a requisition process must follow a determined and standardized flow. Today with the active Internet use, introduction of information technology and cloud computing, the process of requesting material has become much more agile. But at the same time, now it is highly important to trace the responsible for every taken action, to be careful to avoid mistakes, disruptions, fraud, leak of information, etc.
Creating an Efficient Flowchart for Material Requisition in ConceptDraw DIAGRAM
Material Requisition Flowchart can be simply made in ConceptDraw DIAGRAM software as there are all the tools available for you in order to make any kind of it as long as you have a few minutes. Use the Flowcharts solution, which can be found and downloaded from the Diagrams area of ConceptDraw Solution Park on this site, as well as from the ConceptDraw STORE. The last one is another unique product of CS Odessa, which allows choosing any of the existing solutions for many different purposes, including creating the Material requisition flowcharts.
Succeed in drawing using a large quantity of predesigned flowchart-specific shapes, symbols, and icons. All included pre-made design elements can be used in your drawings as well as already-made examples of many kinds of flowcharts, charts, diagrams, schemes, and plans. The Materials flow chart can include a different number of steps. Sometimes the process requires fewer or vice versa more steps as for example in a work with medical, dangerous, rare, or valuable items.
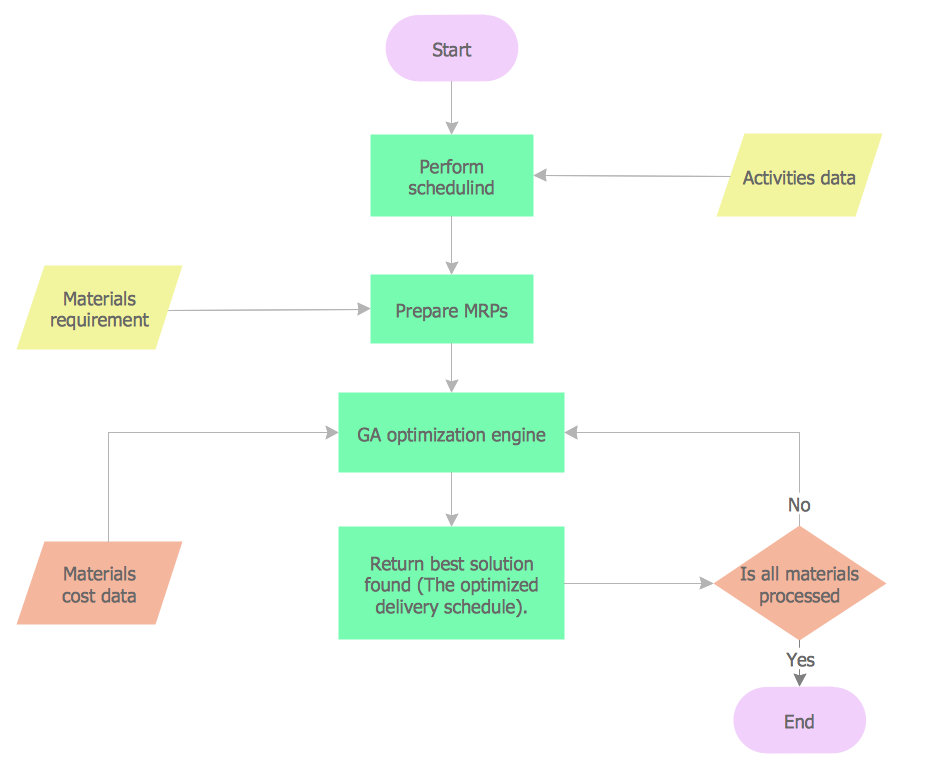
Example 2. Material Flow Chart Example — Material Requisition Flowchart
Conclusion
There are so many Flowcharts that you can use to make explanations for any process, including requisition process and purchase requisition process, and there is a special software that can be used for making these Flowcharts quick and easy — ConceptDraw DIAGRAM diagramming and vector drawing software. Create your own Material requisition flow charts of any degree of detailing using the ConceptDraw DIAGRAM material requisition software extended with the Flowcharts solution from the Diagrams area of ConceptDraw Solution Park fast and easily.
You can find lots of articles describing different drawings on this site, such as Flowcharts, Orgcharts, Business Charts — Area, Line and Scatter, Marketing — Charts and Diagrams, Quality and Manufacturing Charts, Business Process Diagrams — Flow Charts, Marketing — Flowcharts and Process Diagrams, Business Diagrams — Concept Maps, Business processes — Flow charts, Marketing — Flowcharts and Process Diagrams, Finance and Accounting, Marketing — Social Media, Business Diagrams and other, presented in order to help our users to understand what ConceptDraw DIAGRAM application can be used for, besides making Material requisition flowchart.
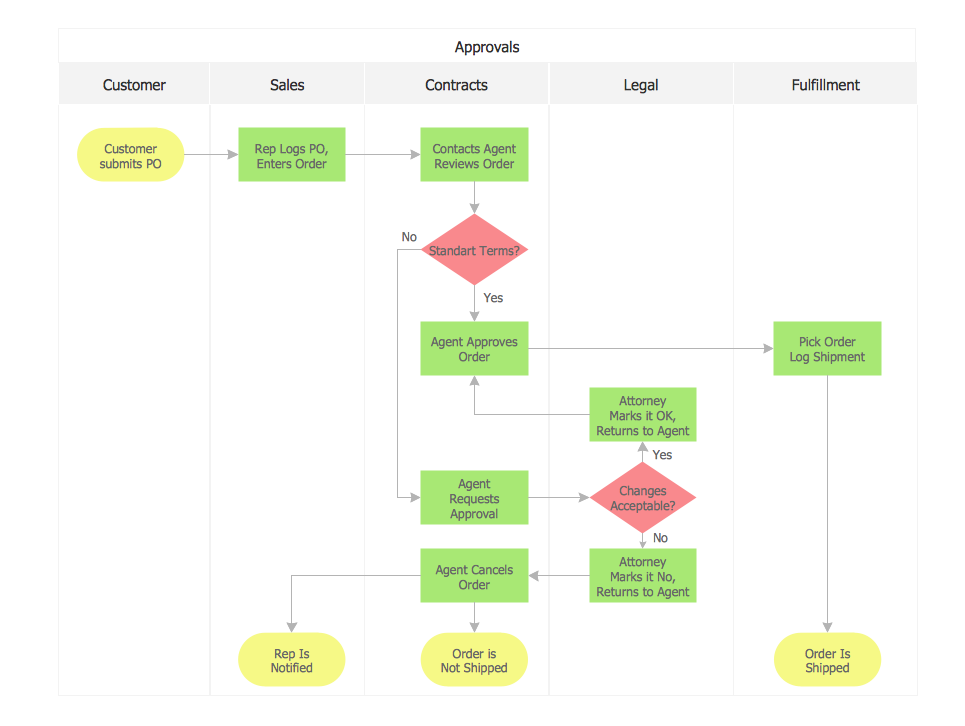
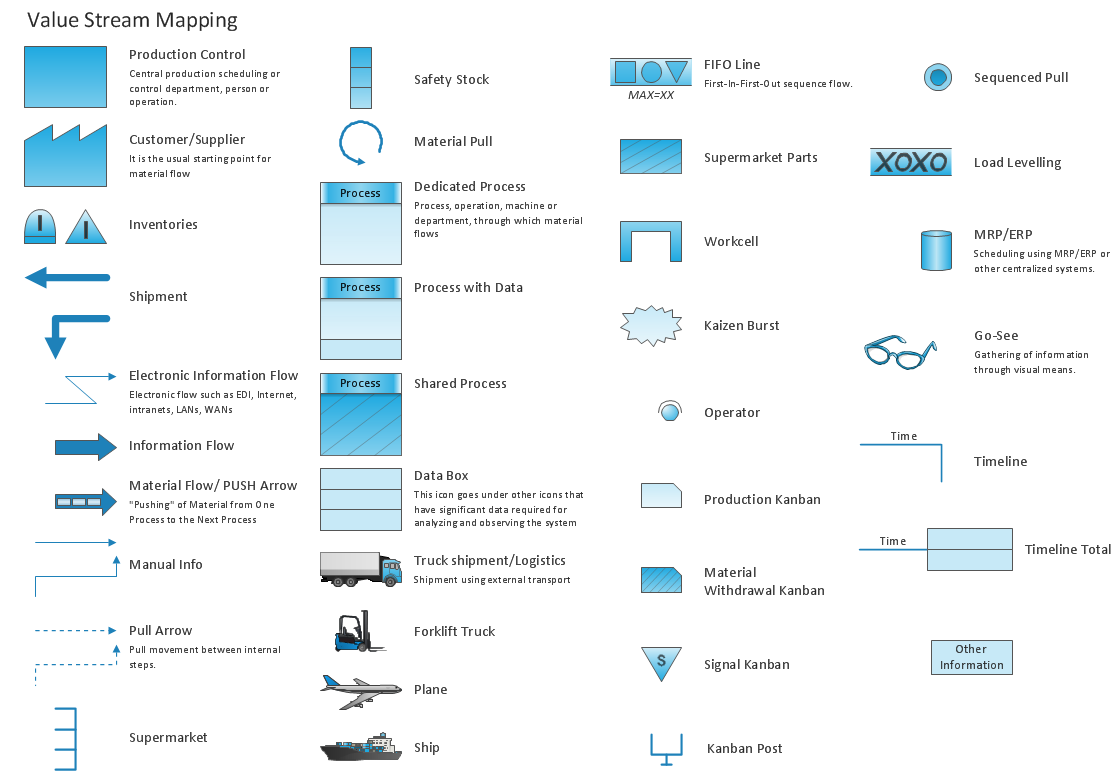
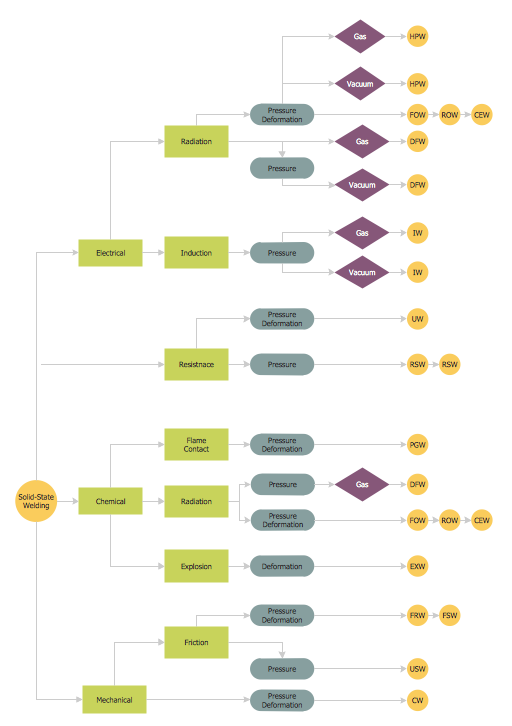
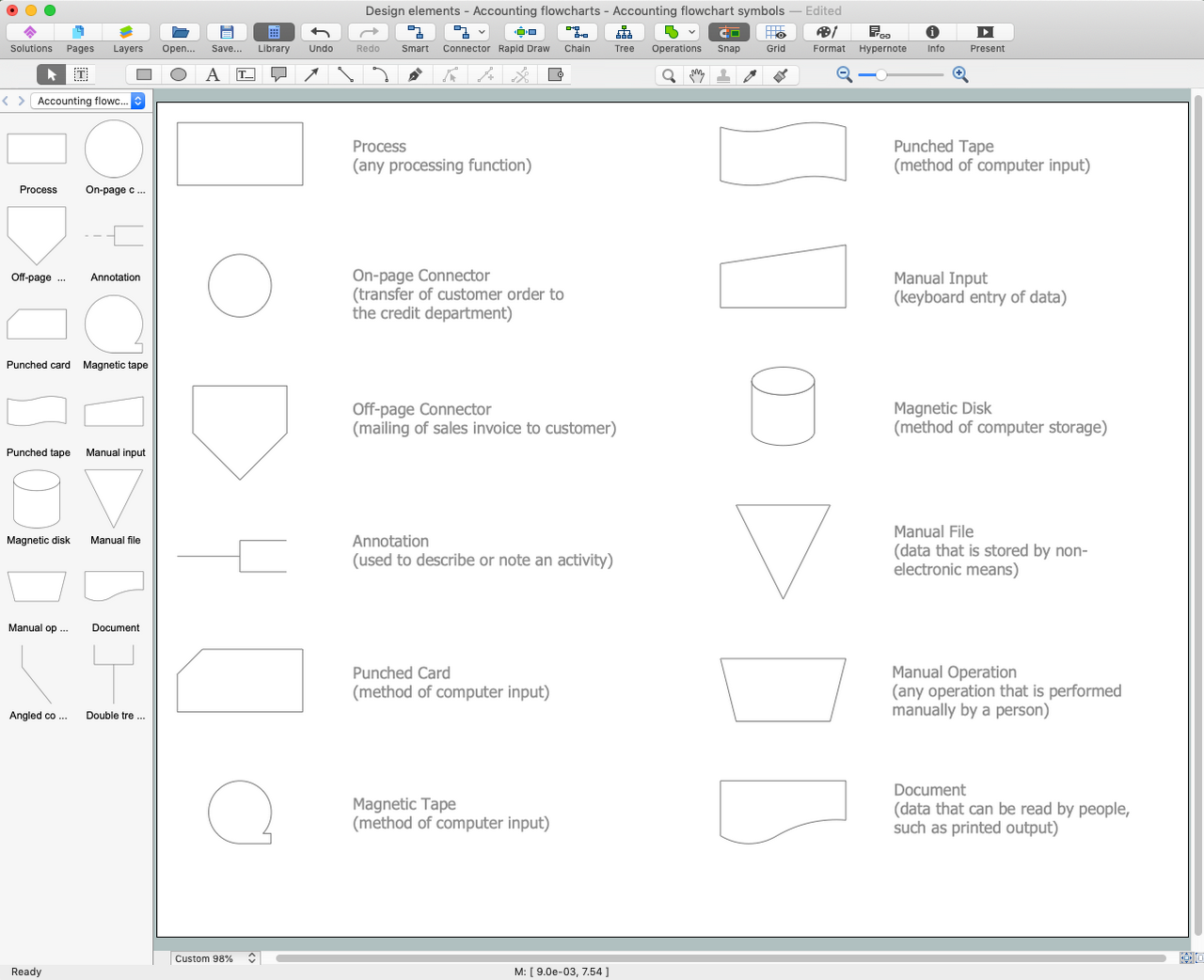
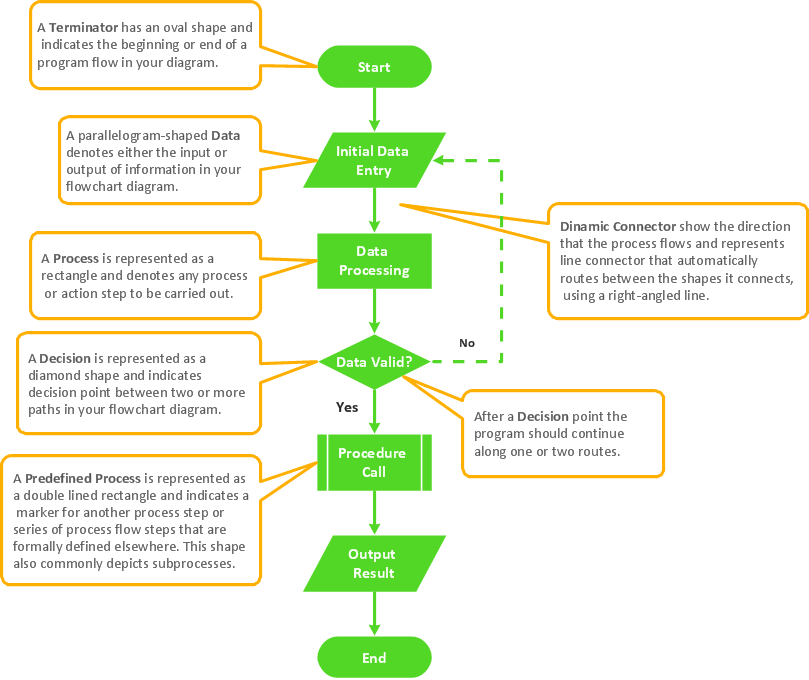
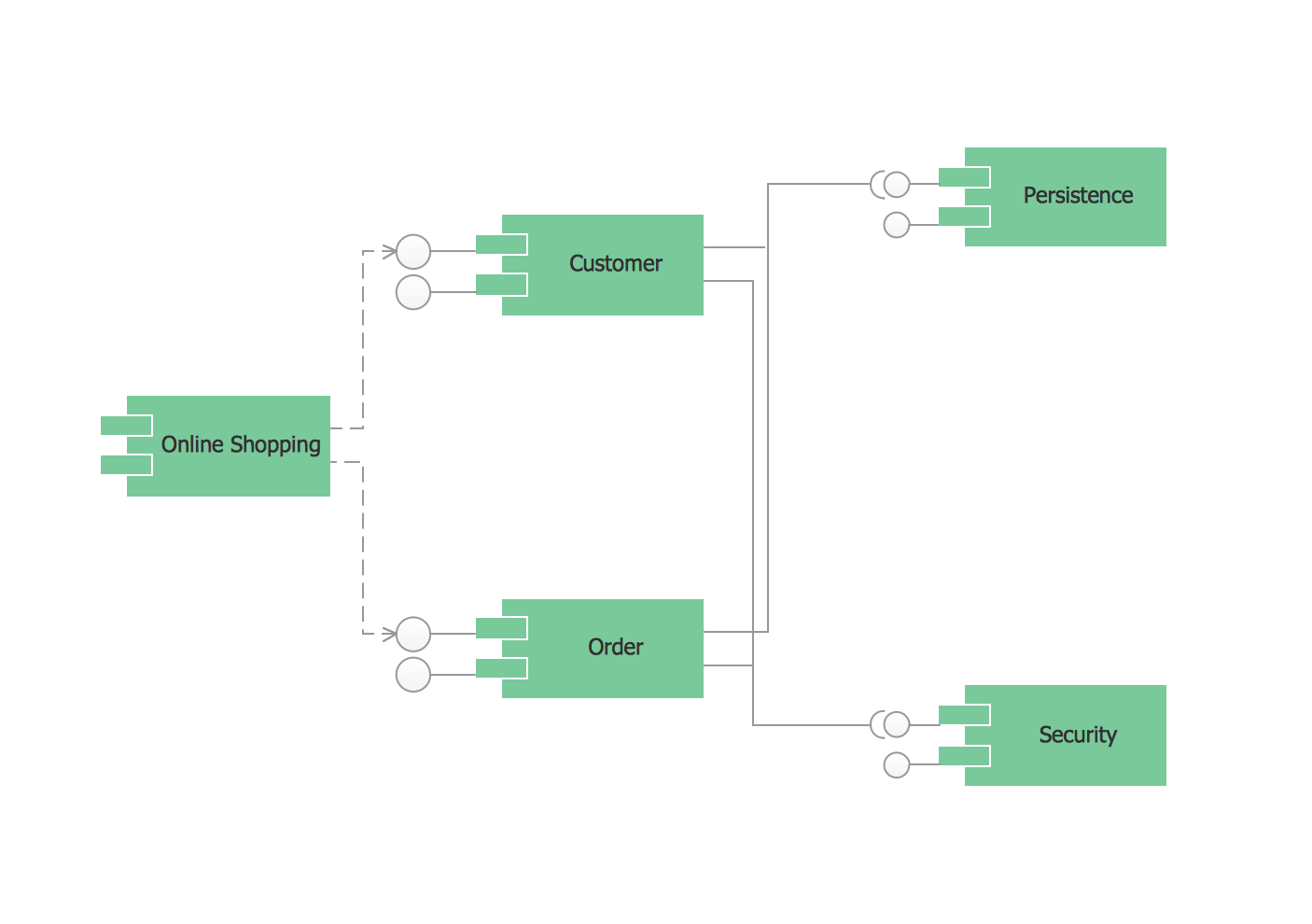
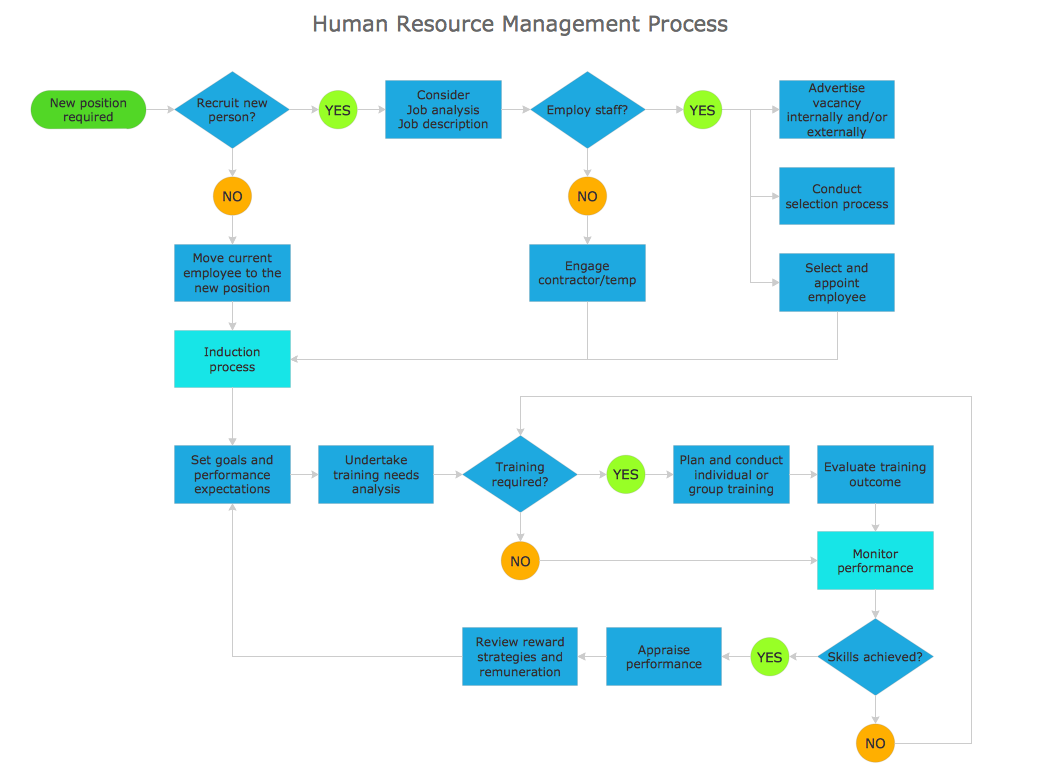
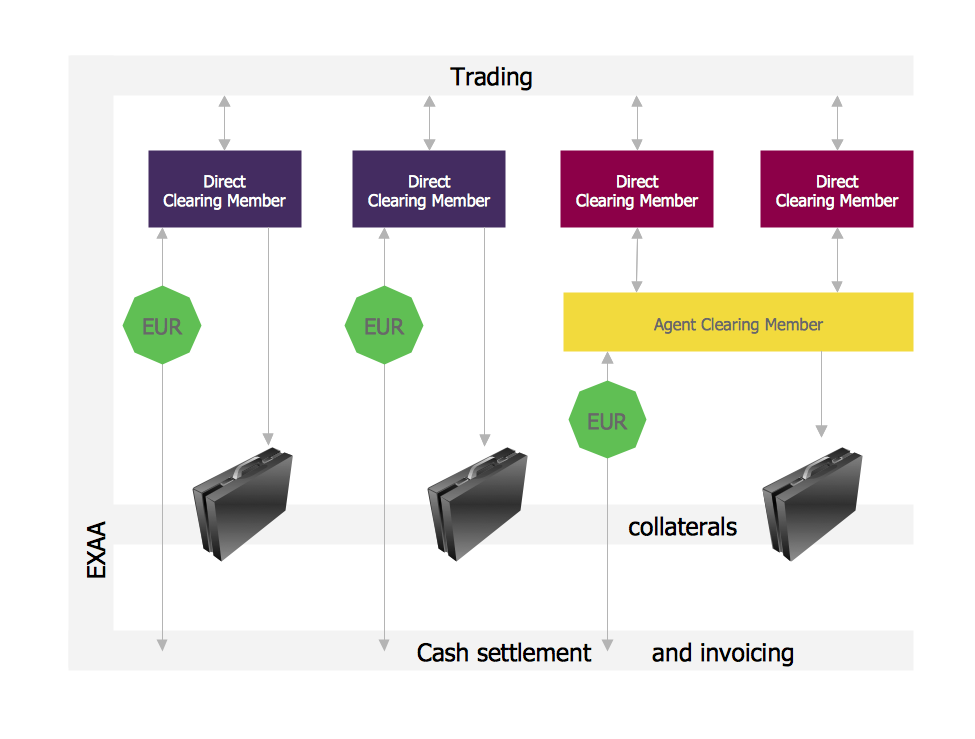