Total Quality Management Definition
Total quality management is the one known to be consisting of some organization-wide efforts put in order to install and to make some climate in which this organization can continuously improve its ability to deliver the high-quality products and services to its customers permanently.
There are no widely agreed-upon approaches within the total quality management activity, that is why all the efforts are known to be drawing heavily on the previously developed techniques and tools of the quality control. Enjoying a widespread attention during the late 1980s as well as the early 1990s before being overshadowed by ISO 9000, Six Sigma and Lean manufacturing, TQM is still a very popular term, especially in the organizations that are focused on making the high-quality goods.
Having no widespread agreement as to what time quality management is as well as what the exact actions that it actually requires of organizations, there is a review of the original United States Navy effort that gives a rough understanding of what it is. Thus, the key concepts in the TQM effort that are undertaken by the Navy in the 1980s include such statements as the quality should be defined by the customers' requirements, top management has the direct responsibility for all the quality improvement and that the increased quality may only come from a systematic analysis as well as a systematic improvement of different work processes within an organization.
Also, the quality improvement within the total quality management definition is known to be a continuous effort as well as a conducted throughout the organization. The Navy used such tools and techniques as the so-called “PDCA cycle” in order to drive different issues to resolution, the ad hoc cross-functional teams that are known to be similar to the quality circles which are responsible for addressing all the immediate process issues, etc.
The previously mentioned techniques used within the TQM also involve arranging the cross-functional teams taking the responsibility for the improvement of the different processes over the long term as well as managing the active participation through steering committees.
Pic.1 Total quality management (TQM) flowchart template
Use of the Seven Basic Tools of Quality for analyzing all the quality-related issues can be an option to go for. Having the need of creating the drawing that may help solve the problems the managers face there is always an opportunity to get a very useful and professionally developed diagramming and drawing software such as the ConceptDraw DIAGRAM one.
The Total Quality Management (TQM) Diagrams Solution is one of many that are available to be downloaded from the ConceptDraw STORE application to be used for making the TQM diagrams as well as many other schemes.
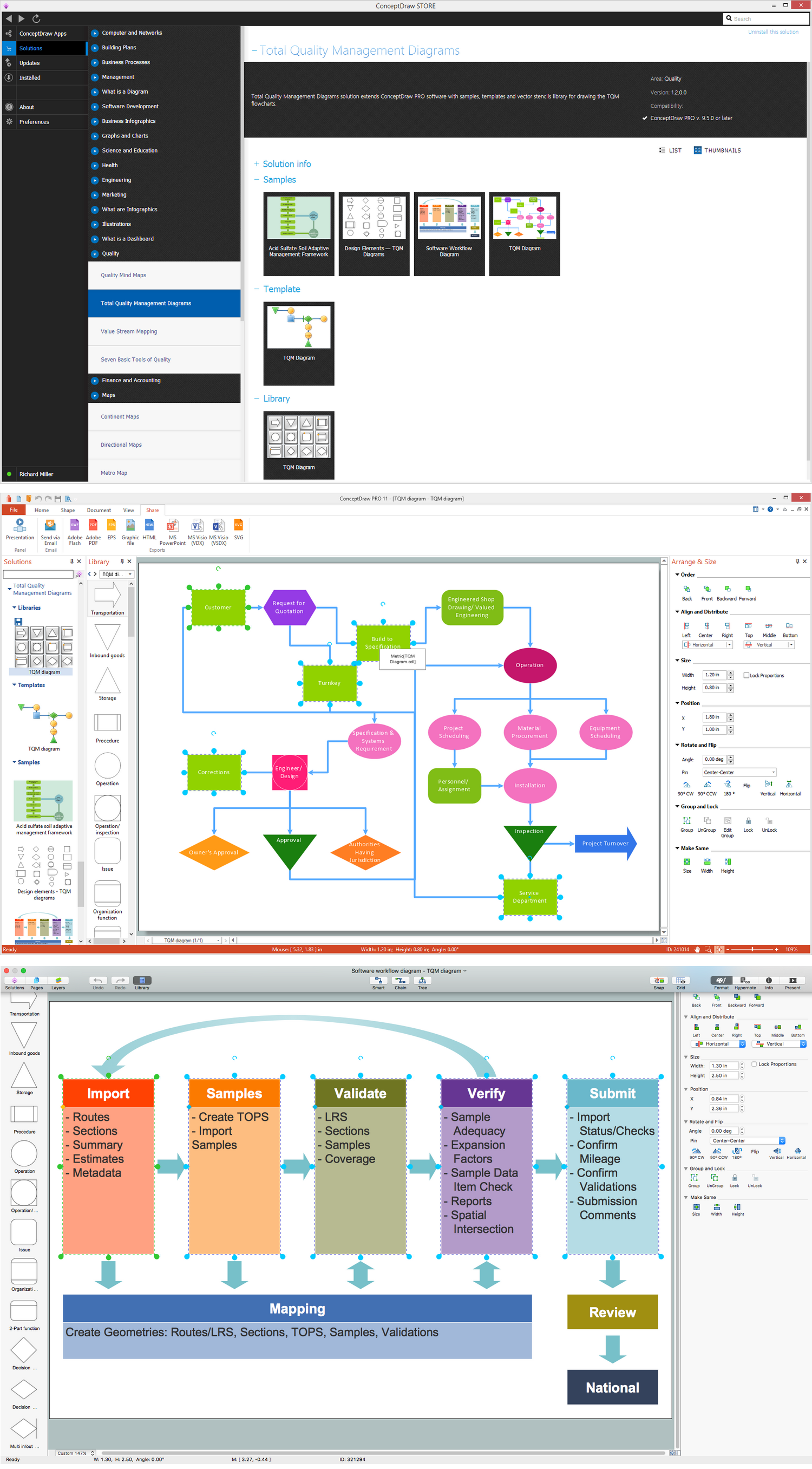
Pic.2 Total quality management (TQM) solution
The Seven Basic Tools of Quality is simply a designation that can be given to some fixed set of different graphical techniques that can be identified as being most helpful in troubleshooting issues being related to quality. Being called “basic”, they are suitable for all those people who do not have as much formal training in statistics. Also, they are called as “basic” for a reason of them being used for solving the vast majority of quality-related issues.
All seven tools are cause-and-effect diagram (it is also known as the Ishikawa or "fishbone" diagram), check sheet, control chart, histogram, Pareto chart, scatter diagram and flow chart (also known as “run chart”). Making any of the mentioned drawings with the help of the ConceptDraw STORE application, and the Total Quality Management (TQM) Diagrams Solution in particular, can take only a few minutes as using all the previously created templates is easy making the new charts in this way.
Some of the TQM tools were possibly introduced by Kaoru Ishikawa who was known to be influenced by a series of lectures of W. Edwards Deming that had been given to the Japanese engineers and scientists in 1950. At that time, those companies that had some problems in training their workforces in a statistical quality control were found that the complexity of the subject intimidated the vast majority of their workers scaling back the training in order to focus on the simpler methods which suffice for most quality-related issues.
The Seven Basic Tools are known to be standing in a contrast to more advanced statistical methods. Such methods may be surveyed sampling, statistical hypothesis testing, the design of experiments, acceptance sampling, multivariate analysis and other During the 1990s, most of the standards bodies from Belgium, Germany, France, the United Kingdom and Turkey attempted to standardize total quality management. While many of the mentioned standards have since been already withdrawn, they all are still effectively superseded by ISO 9000.methods that were developed in the field of operations research.
The Project Management Institute is known to be referring the Seven Basic Tools in A Guide to the Project Management Body of Knowledge. It was done to make an example of a set of the most general tools that were accepted to be useful for controlling and planning the project quality.
During the 1990s, most of the standards bodies from Belgium, Germany, France, the United Kingdom and Turkey attempted to standardize total quality management. While many of the mentioned standards have since been already withdrawn, they all are still effectively superseded by ISO 9000.
The definition of the total quality management was given in this article but to actually get down to making the needed TQM drawing, such as a TQM diagram, all the needed tools can be found in the Total Quality Management (TQM) Diagrams Solution from the ConceptDraw STORE application to be used in the ConceptDraw DIAGRAM diagramming and drawing application.
TEN RELATED HOW TO's:
When moving to a new apartment it is always pleasure to develop an interior design project. Nevertheless, another important part that should not be forgotten is the piping plan, because wrong piping system might ruin all the renovation. So, to avoid such problems, a stress analysis is performed.
Plumbing and piping plans should be created for any premises. They are used to trace location of pipes, fixtures and valves in the house. This diagram presents a set of certified piping plan symbols for drawing plumbing and piping floor plans, diagrams and other technical drawings. Applying standard symbols when creating a piping plan is very important for creating a valid piping plan included into the building documentation pack. It is essential for any professional to be able to read and properly interpreted any piping plan.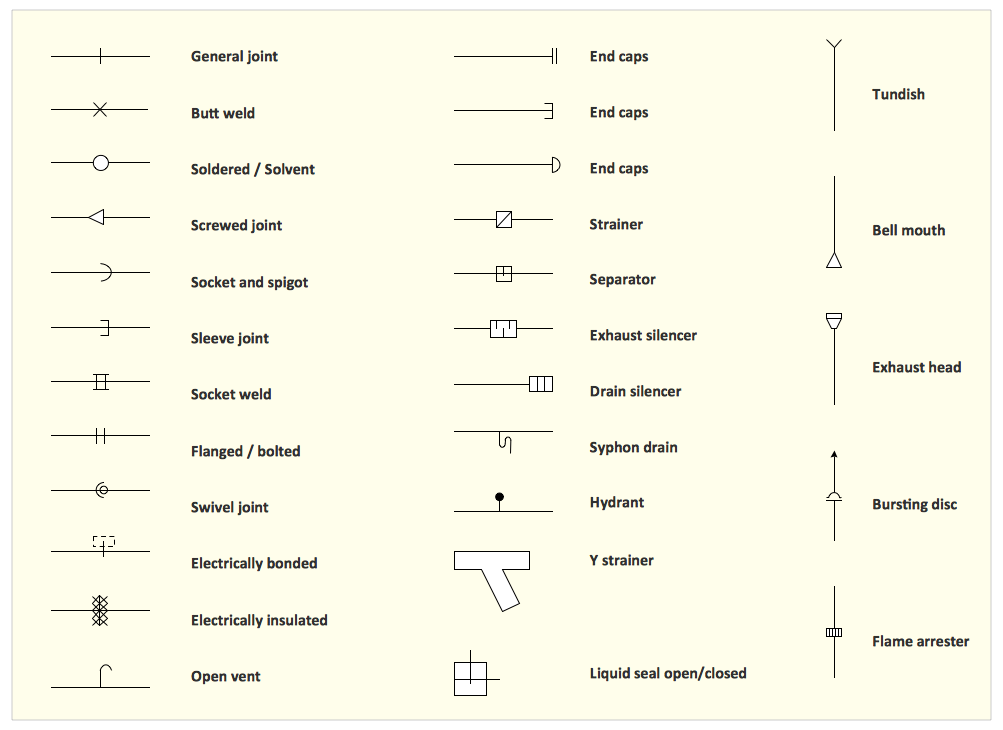
Picture: Interior Design. Piping Plan — Design Elements
Related Solution:
ConceptDraw DIAGRAM diagramming and vector drawing software enhanced with Total Quality Management (TQM) Diagrams solution from the Quality area of ConceptDraw Solution Park is rich for the useful and effective TQM tools.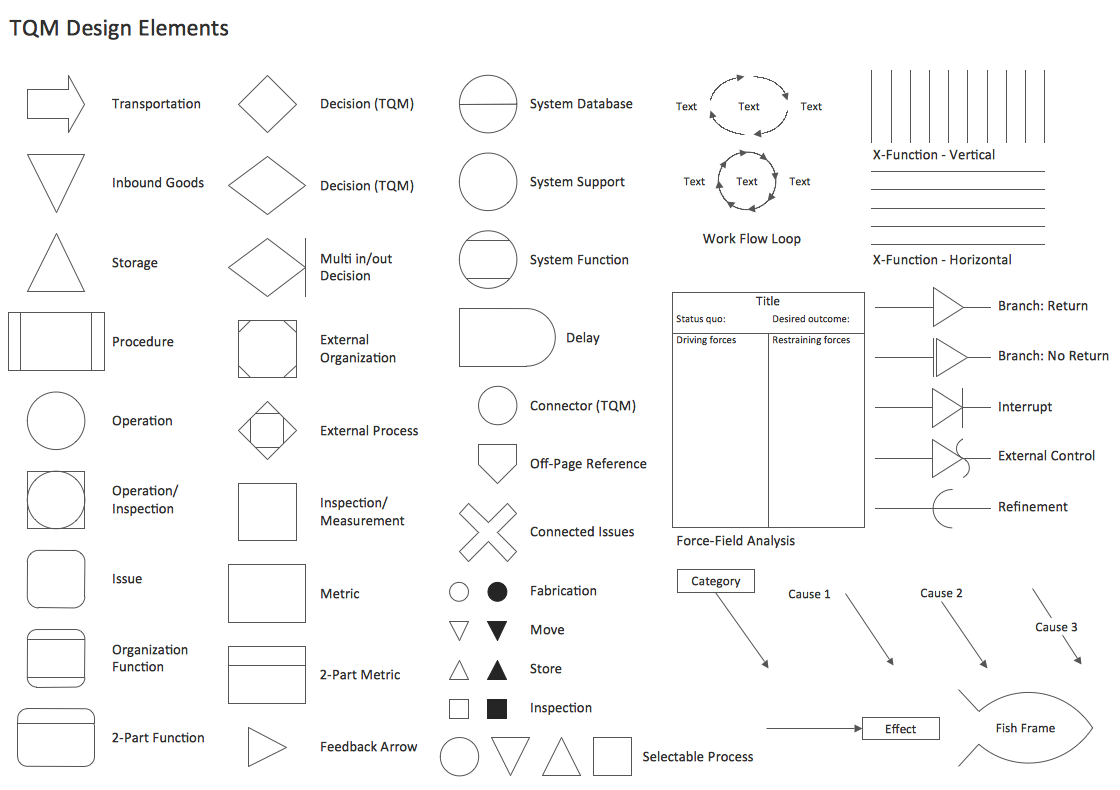
Picture: TQM Tools
Related Solution:
ConceptDraw MINDMAP with the ability to import presentations from Microsoft PowerPoint, as well as enhancing its existing presentation capabilities.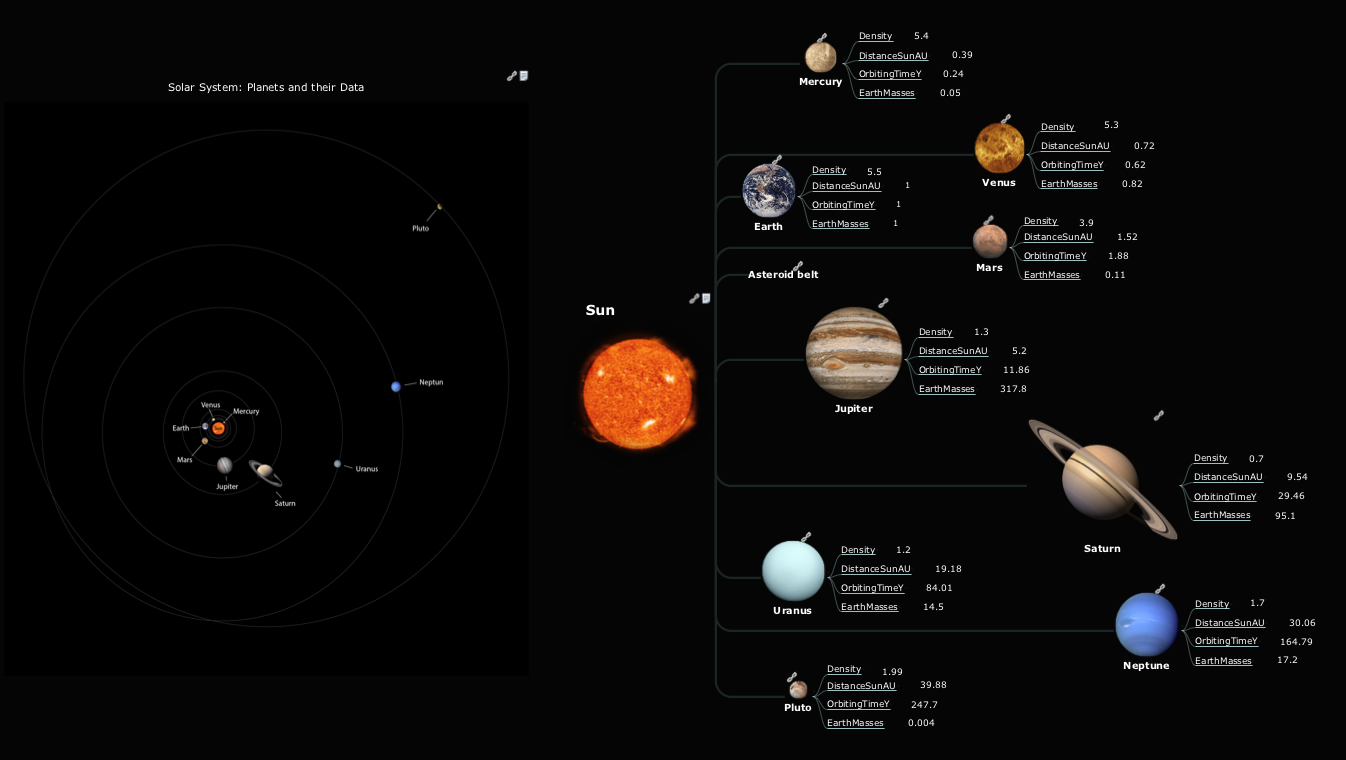
Picture: Best Mind Mapping Program for Making Presentations
Related Solution:
A competent delegation of responsibilities between workers guarantees business success in most cases. At first sight, it might seem that workflow diagram symbols are quite similar to a regular flowchart. But workflow diagram is a more accurate way to present working processes.
Workflow diagrams are helpful for a working process analyzation, to depict a pathway of process issues, personalize responsibilities and identify resources that will help to optimize a workflow. Generally, Workflow diagram deploys flowchart symbols for displaying work process steps and relationships. But, often it require some additions and improvements to become more professional and illustrative. The Workflow solution for ConceptDraw DIAGRAM provides the user with a big library of symbols that are designed especially for workflow diagrams.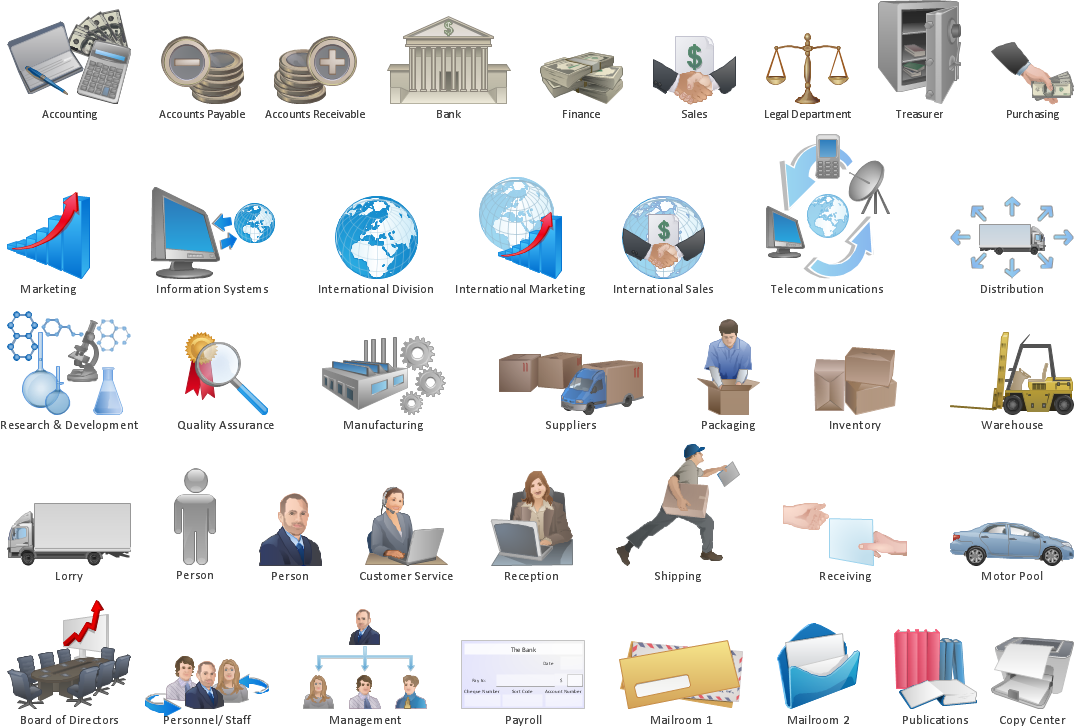
Picture: Workflow Diagram Symbols
Related Solution:
In software engineering, it is important to understand how the system would cooperate with external sources, like data sources. To give this information a visual representation, data flow diagrams (DFD) were used for years. The entire system is usually divided into smaller ones, and all of them process data flows in appropriate ways.
The visualizing business processes which engages the data transfer, is commonly preformed using DFDs (data flow diagrams). DFD is used to show the data flow processing and transformation. This DFD represents the electronic system of a customer purchase. It was created using Gane/Sarson notation. Data flow diagrams helps you to sort through and clarify transferring process making it available for analysis, and representation. ConceptDraw DFD solution introduces the vector library, containing the full set of icons from DFD notations.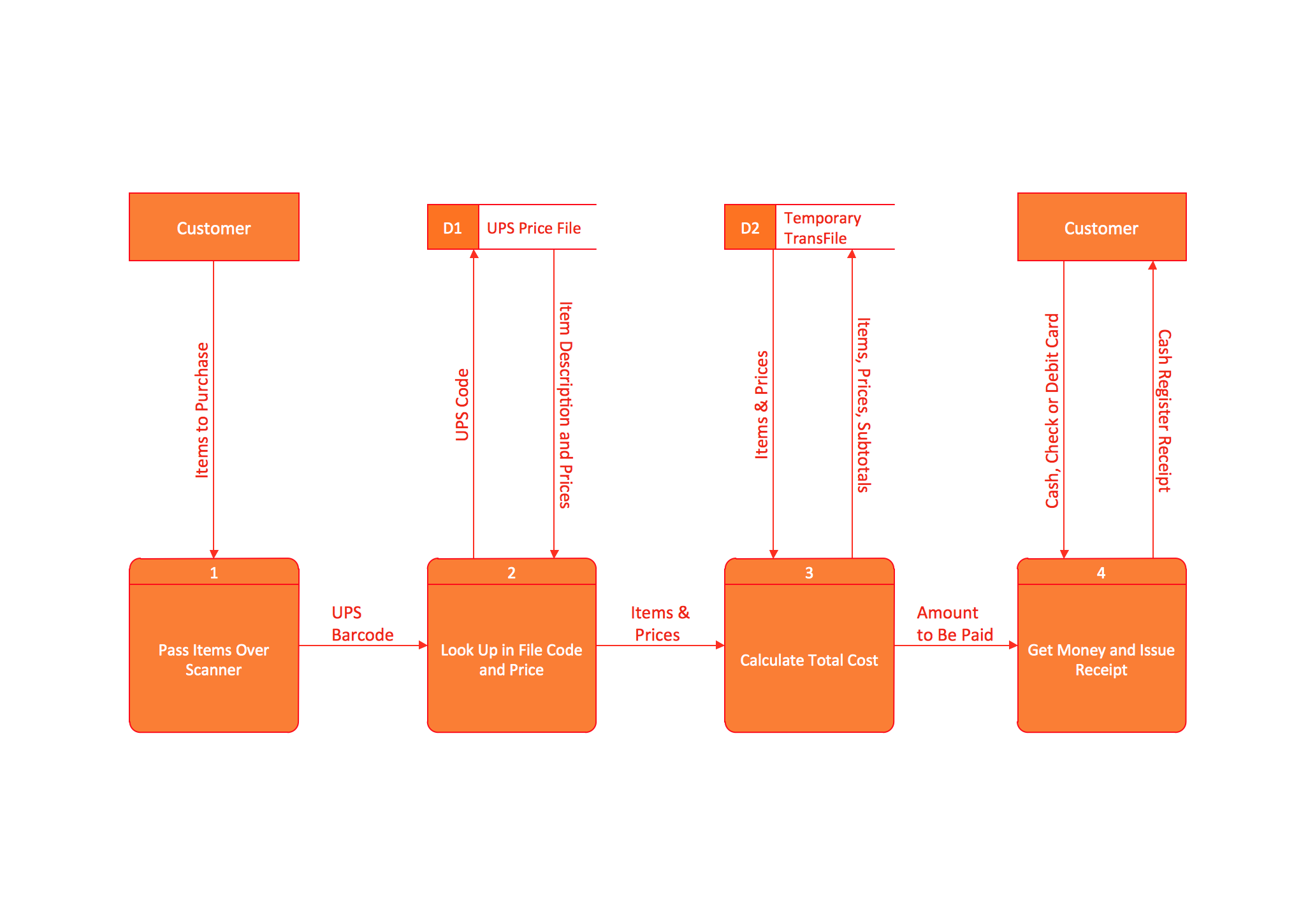
Picture: Data Flow Diagram (DFD)
Related Solution:
Electrical rotating machines, such as motors and generators, are vital assets for any power plant or large industrial company.
An electric motor is an electrical machine that converts electrical energy into mechanical energy. The reverse of this would be the conversion of mechanical energy into electrical energy and is done by an electric generator.
In normal motoring mode, most electric motors operate through the interaction between an electric motor's magnetic field and winding currents to generate force within the motor. In certain applications, such as in the transportation industry with traction motors, electric motors can operate in both motoring and generating or braking modes to also produce electrical energy from mechanical energy.
26 libraries of the Electrical Engineering Solution of ConceptDraw DIAGRAM make your electrical diagramming simple, efficient, and effective. You can simply and quickly drop the ready-to-use objects from libraries into your document to create the electrical diagram.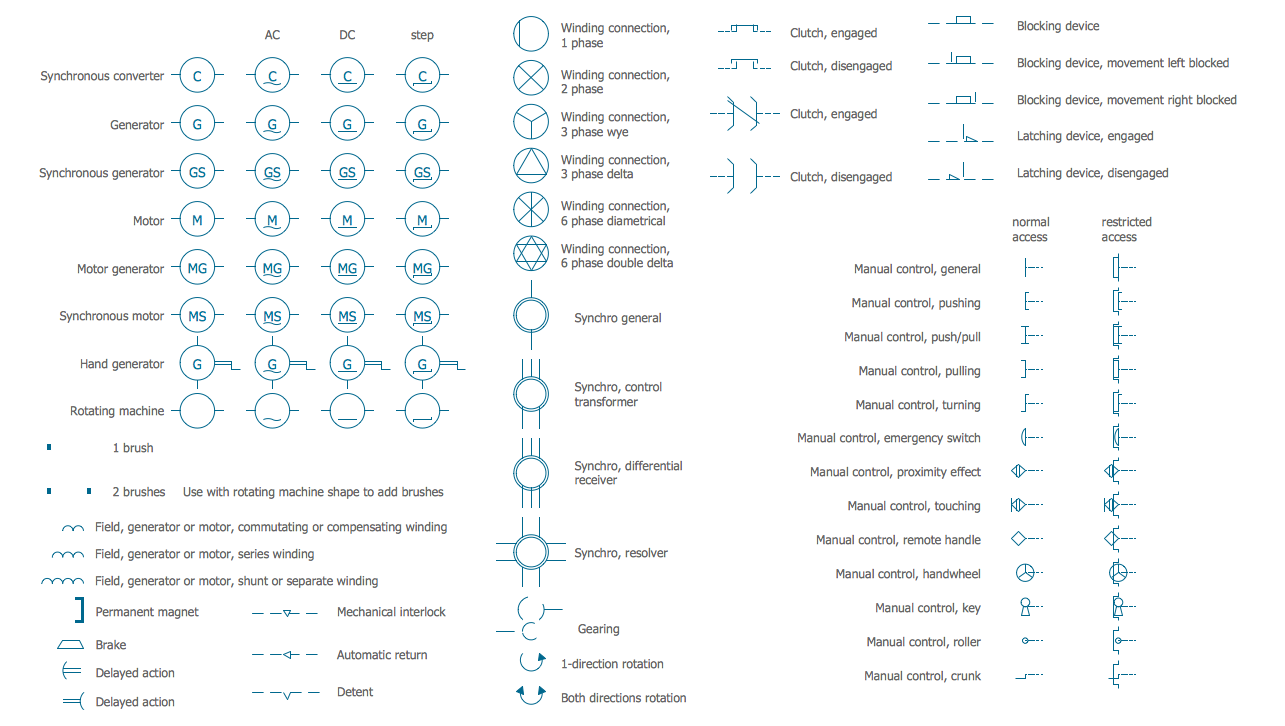
Picture: Electrical Symbols — Rotating Equipment
Related Solution:
Diagramming is an astonishing way to visualize business processes. The list of the most common business process flowchart symbols is quite long starting from basic flowcharts, continuing with SIPOC diagrams. Business process modeling was never easier than now, with special ConceptDraw Business Process Mapping solution.
To carry out all professional standard requirements for business processes mapping, it is necessarily to follow the special graphical notations. ConceptDraw Business Process Mapping solution offers an exhaustive suite of tools to aid business process mapping. There are three vector libraries SIPOC Diagrams, Business Process Flowcharts, and Swim Lanes that contains totally more than 50 symbols of standard BPM notations. This is all that professionals need to effectively evaluate and manage quality in business processes.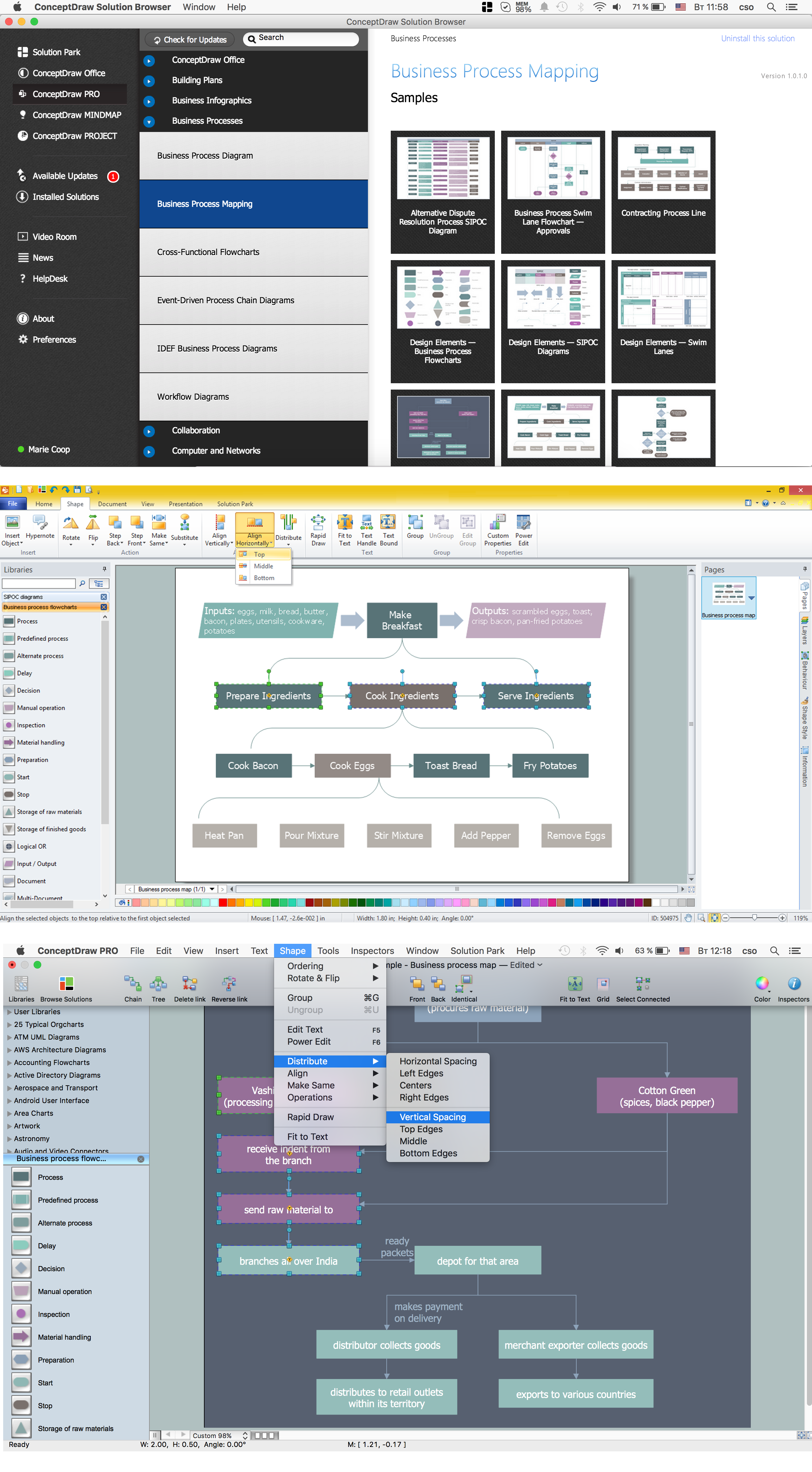
Picture: Business Process Flowchart Symbols
Related Solution:
Social media is a popular view of mass communication which allows people, companies and organizations create, share, discover, modify, access, comment, discuss and exchange information through the Internet. Social Media Response solution for ConceptDraw DIAGRAM provides collection of 10 libraries with diversity of predesigned vector social media flowchart symbols for fast and easy creating interactive Social Media Flowcharts, Response Charts and Action Mind Maps.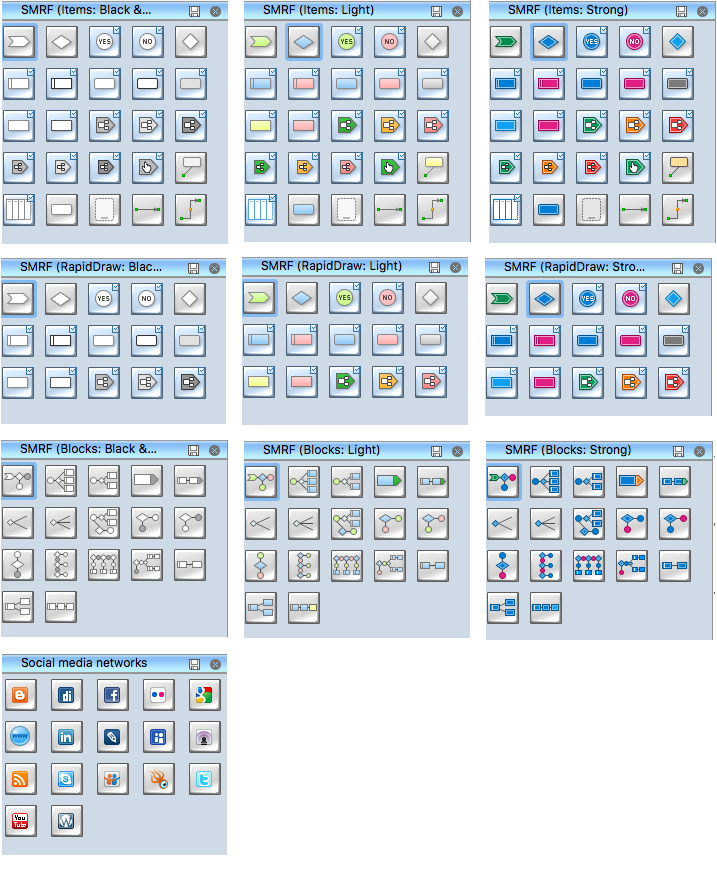
Picture: Social Media Flowchart Symbols
Related Solution:
Developing Restaurant Layouts is very important and responsible moment in restaurant construction and designing. Now it's very simple and fast process thanks to the Cafe and Restaurant Floor Plans solution from the Building Plans area of ConceptDraw Solution Park.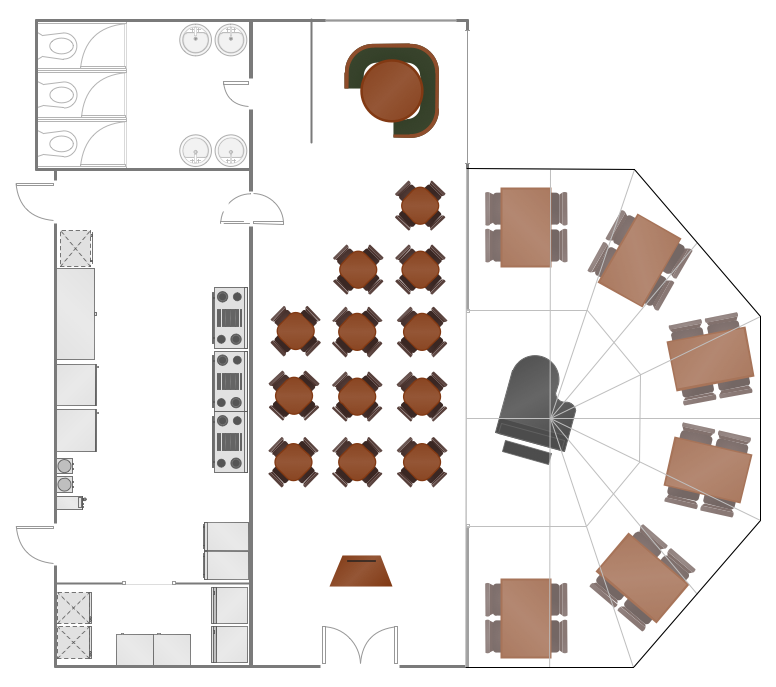
Picture: Restaurant Layouts
Related Solution: